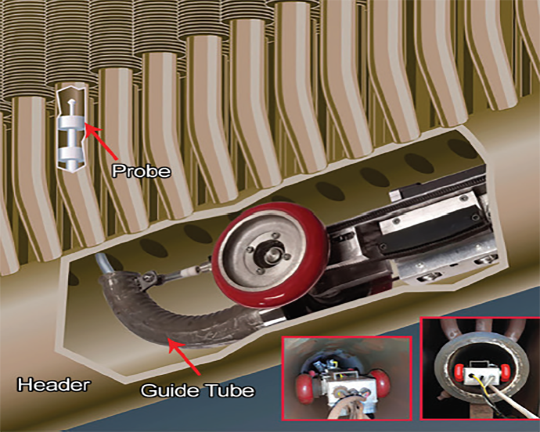
- If there is a piece of equipment or object that you need inspected, and it is constructed of metal, our Solution Providers Group (SPG) is ready to help you come up with a way to inspect it. Whether that means coming up with a way to modify existing technology to suit your needs, or coming up with new technologies to meet them, the SPG is there to help.
- Some reasons a traditional inspection may not be possible include:
- Inaccessibility
- Eliminating radioactive hazards
- Reducing difficult or impractical configurations, like hydro testing
- Unforeseen compositional changes in the material
- Whatever the reason, the SPG is designed to leverage our field service knowledge to create a solution for your needs. In the past we have developed specialized robotics, probes and testing procedures to ensure a fast, accurate and cost effective solution to meet our clients’ needs.
Solution Providers Group (SPG)
- The Balanced Field Electromagnetic Technique (BFET) can detect corrosion fatigue cracking by sending an electromagnetic signal into the metal. A detector coil measures any change in the signal and can size cracking within 10% accuracy through the use of calibration standards. TesTex has developed and customized a internal rotating BFET probe for sizing corrosion fatigue cracking. This probe is able to travel through bends for boiler tubes with a inside tube diameter of 2″ or greater.
Corrosion Fatigue Cracking Inspections at OVEC
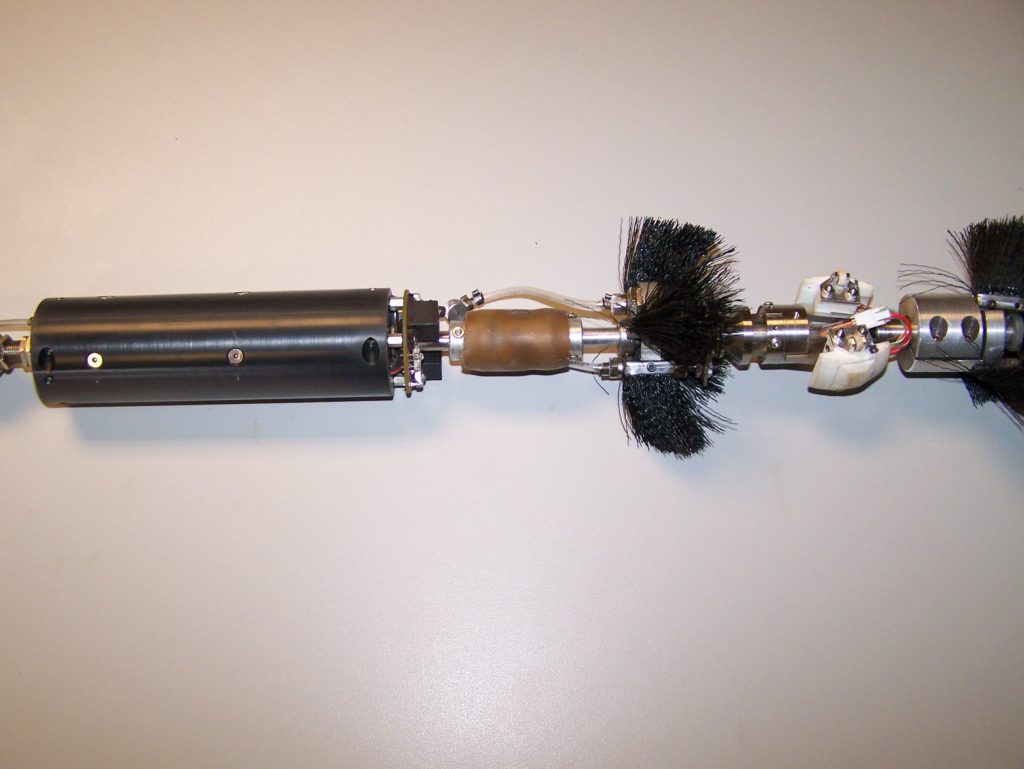
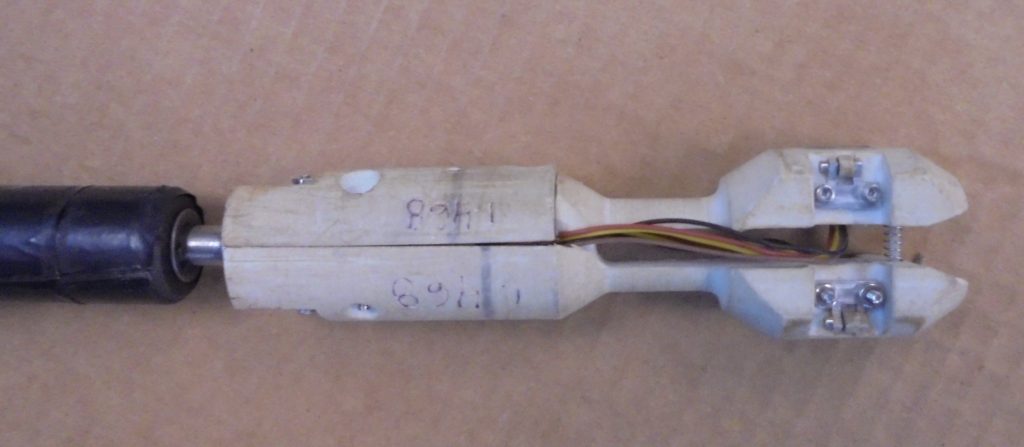
- For smaller diameter tubes, TesTex developed a rotating probe to examine the straight sections for corrosion fatigue cracking. Each size tube and wall thickness takes a specially designed probe to ensure proper expansion of BFET sensors for optimal results.
- TesTex also has a Multi Channel BFET probe that is used as a screening tool for detecting cracks in boiler tubes from the inside surface.
- TesTex uses a Borescope to inspect the tube for cracks and notes any locations. Once the locations are noted, the BFET probe is inserted and pushed to that location. The rotating BFET probe measures the signal response to size the depth of the cracking.
Corrosion Fatigue Cracking Inspections at LG&E
- TesTex developed handheld BFET probes to scan the outside diameter of a tube or pipe looking for graphitization. Quality readings can be acquired through coatings such as paint and uniform scale. The actual probe does not need to be in contact with the test piece. BFET is able to locate areas suspected of containing graphitization. Core samples are removed at select locations found with the BFET for further analysis.
Graphitization Inspection (NRG, EPRI)
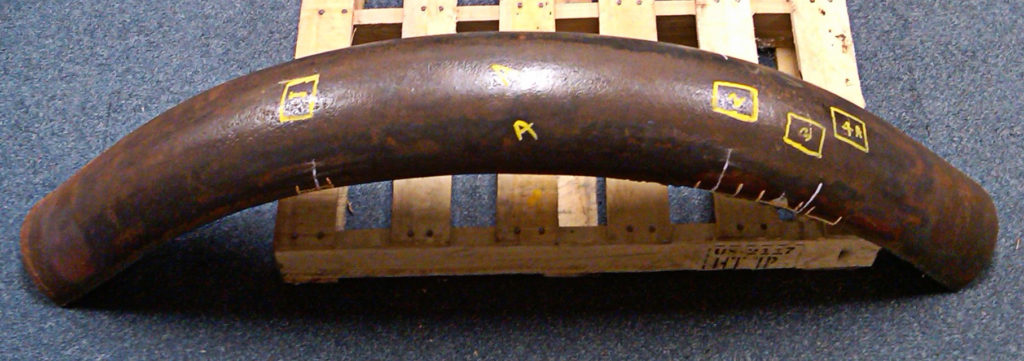
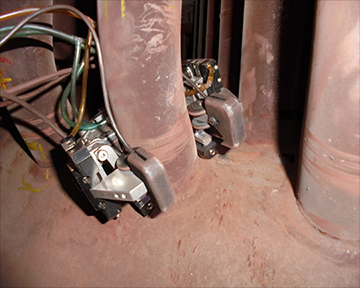
- TesTex adapted the Balanced Field Electromagnetic Technique (BFET) to detect tube to header weld cracking in HRSG units. BFET sensors and cameras are placed on the welds using a C-clamp housing called “The Claw” that attaches to the tube. Once attached to the tube, the Claw moves circumferentially around the weld to detect cracking, lack of fusion undercut, porosity and other defects. The Claw can be customized to inspect 1.5″ – 3.0″ diameters.
Tube to Header Weld Cracking – HRSG Claw
- The Low Frequency Electromagnetic Technique (LFET) can detect and quantify wall thinning on HRSG finned tubes from the outside surface through the fins. As the LFET scanner moves along the tube surface, it measures the strength of the return signal that is transmitted into the tube by the scanner’s exciter coil. This technology is able to detect both localized and general wall loss such as pitting, under deposit corrosion and flow accelerated corrosion.
Wall Thinning – HRSG LFET
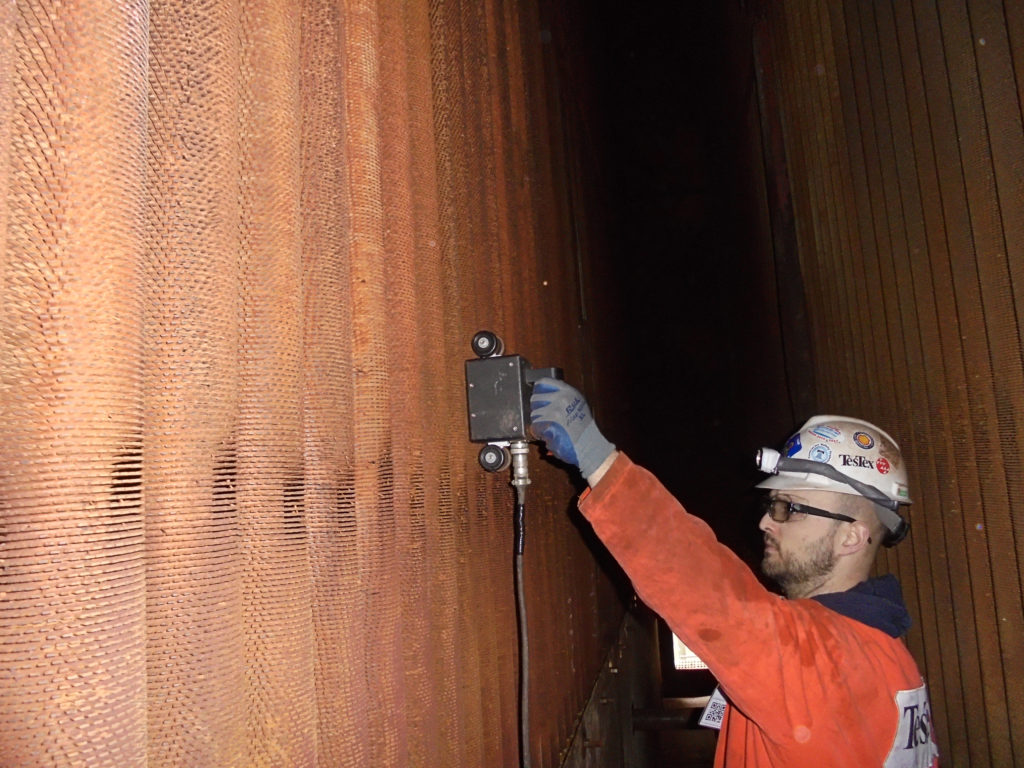
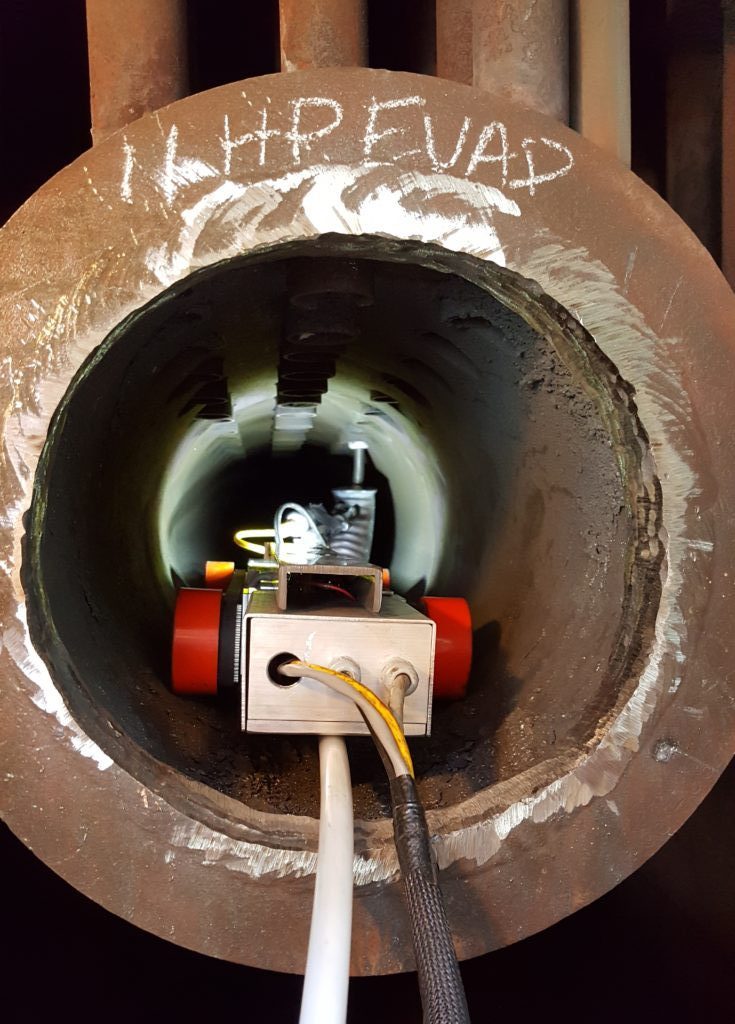
- TesTex developed an Internal Access Tool for inspections of HRSG tubes upon removal of the end cap. The crawler is placed inside the header. A probe is mechanically inserted into each tube to detect tube corrosion/pitting and capture video of the inside surface of the tube. A modest amount of scale buildup inside of the tube is acceptable for the inspection.
Internal Tube Inspection – HRSG Internal Access Tool (IAT)
- A major coal fired power plant in West Virginia contacted TesTex to locate seam welds in a 24″ return line during an outage. TesTex modified the Low Frequency Electromagnetic Technique (LFET) scanner for seam weld detection in pipelines and headers. The overall objective of this project was to detect ground down seam welds in carbon steel and low-alloy steel piping and to pinpoint the exact location on the pipe.
Seam Weld Detection (EPRI, AEP, NRG)
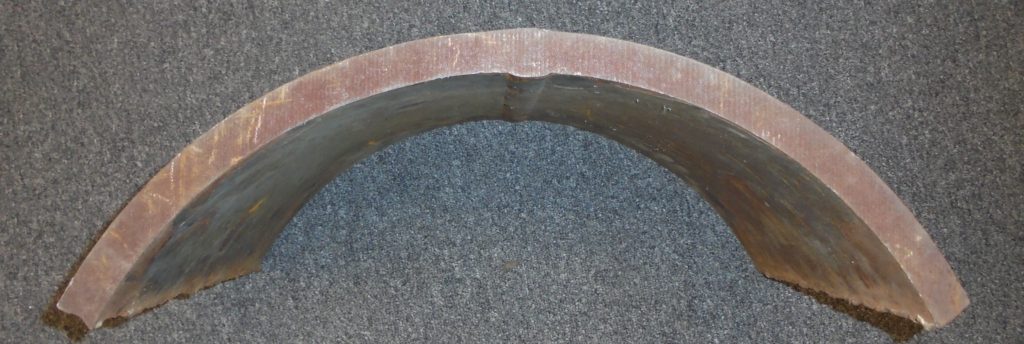
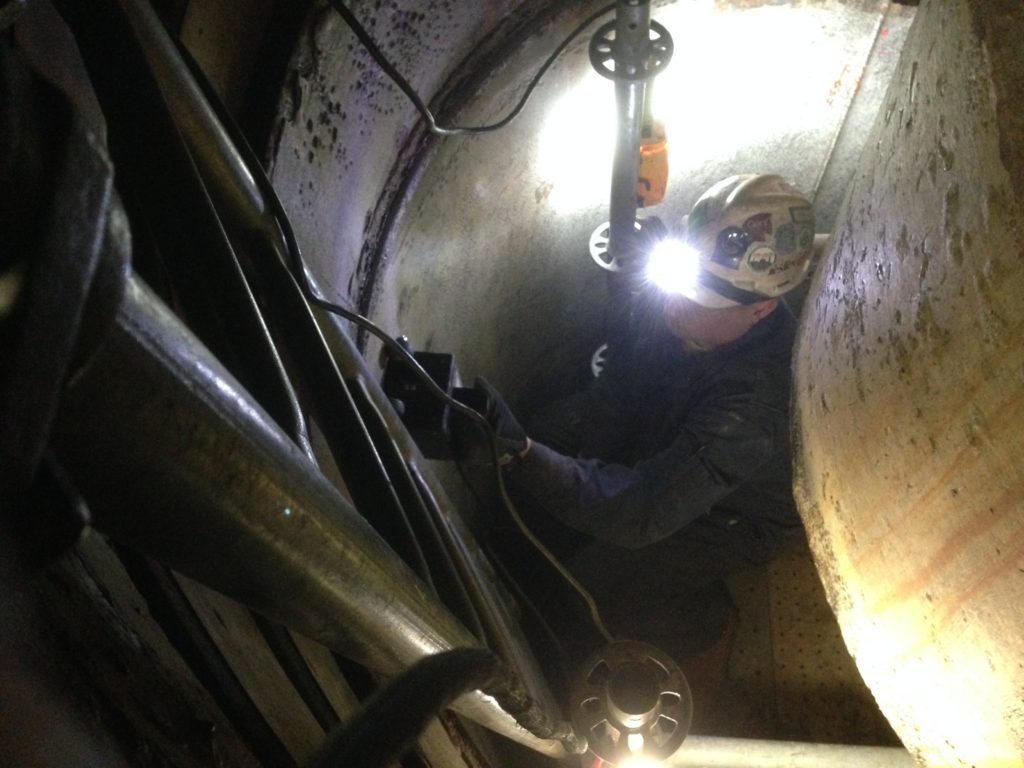
- TesTex developed special contoured Low Frequency Electromagnetic Technique (LFET) scanners for circulating water line inspections. These scanners are used to scan the inside of circulating water lines where they penetrate concrete floors. These pipes can experience corrosion on the outside diameter at these concrete penetrations and can flood the basement of the power plant quickly if a leak occurs. TesTex also offers an internal visual inspection of the circulating water lines from the condenser to the cooling tower using API 570 inspections.
Circulating Water Line Inspection (XCEL)
- TesTex adapted the Balanced Field Electromagnetic Technique (BFET) to detect internal cracking in gen bank tubes. Circumferential cracking is detected in boiler tubes from the ID of the tube. Through the use of a calibration standard, TesTex is able to provide an approximate crack depth.
Internal Cracking in Gen Bank Tubes – Pure Energy (TELOGIA POWER)
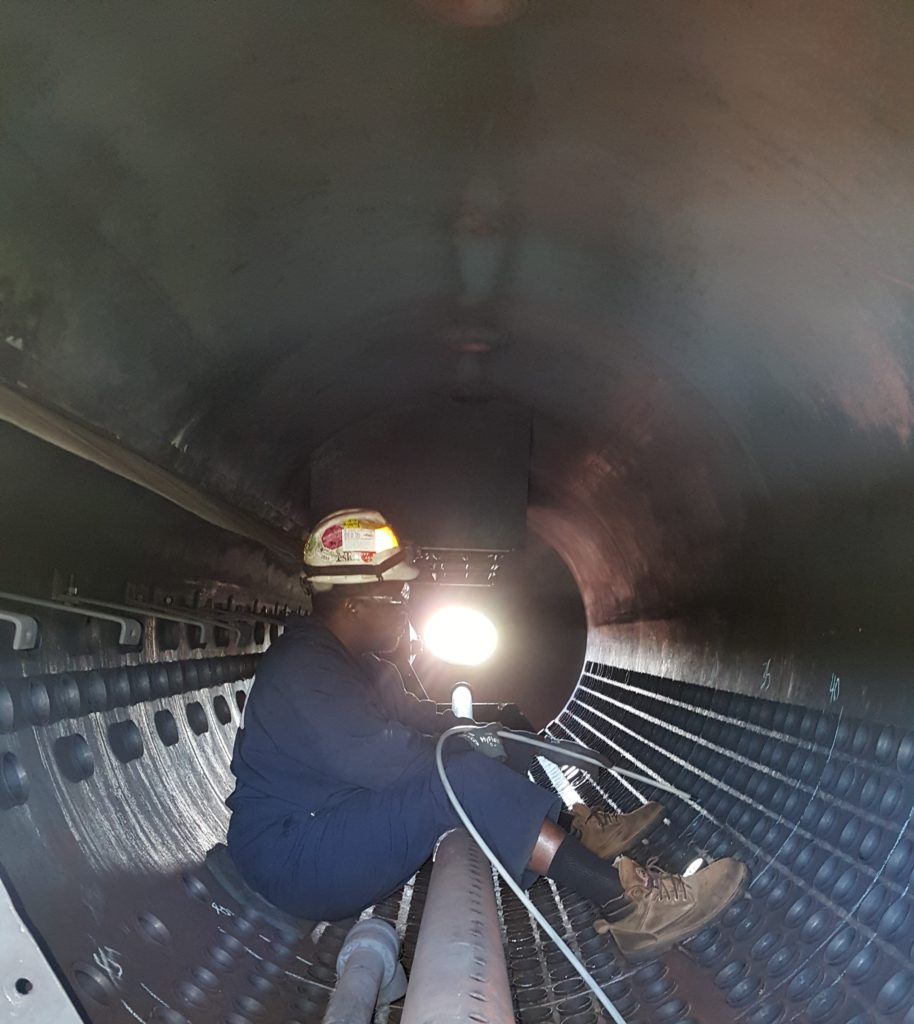
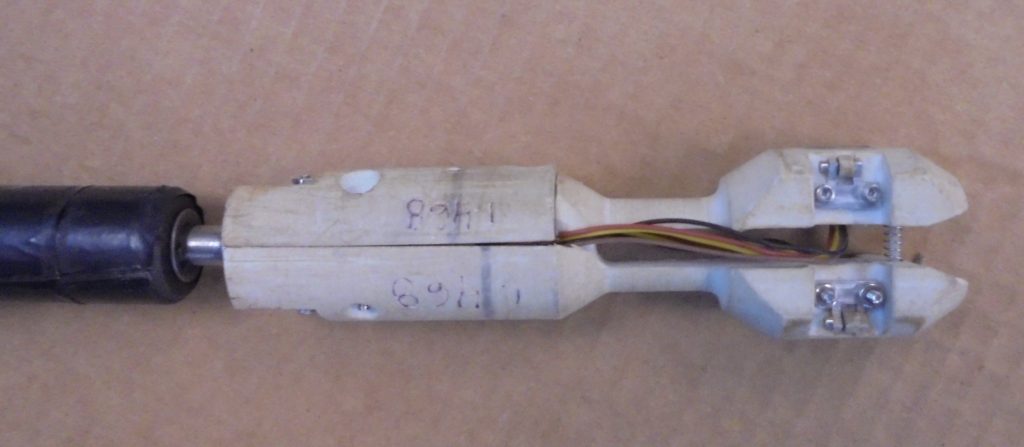
- TesTex designed a two channel rotating Balanced Field Electromagnetic Technique (BFET) probe for cracking and lap weld inspection. The probe takes cross sectional readings throughout the entire straight section of a tube. This inspection was performed to look for manufacturing defects in new superheater assemblies. TesTex records the readings and notes any indications that would need further evaluation.