Detecting Cracks Not Visible with Dye Penetrant
4/4/2016
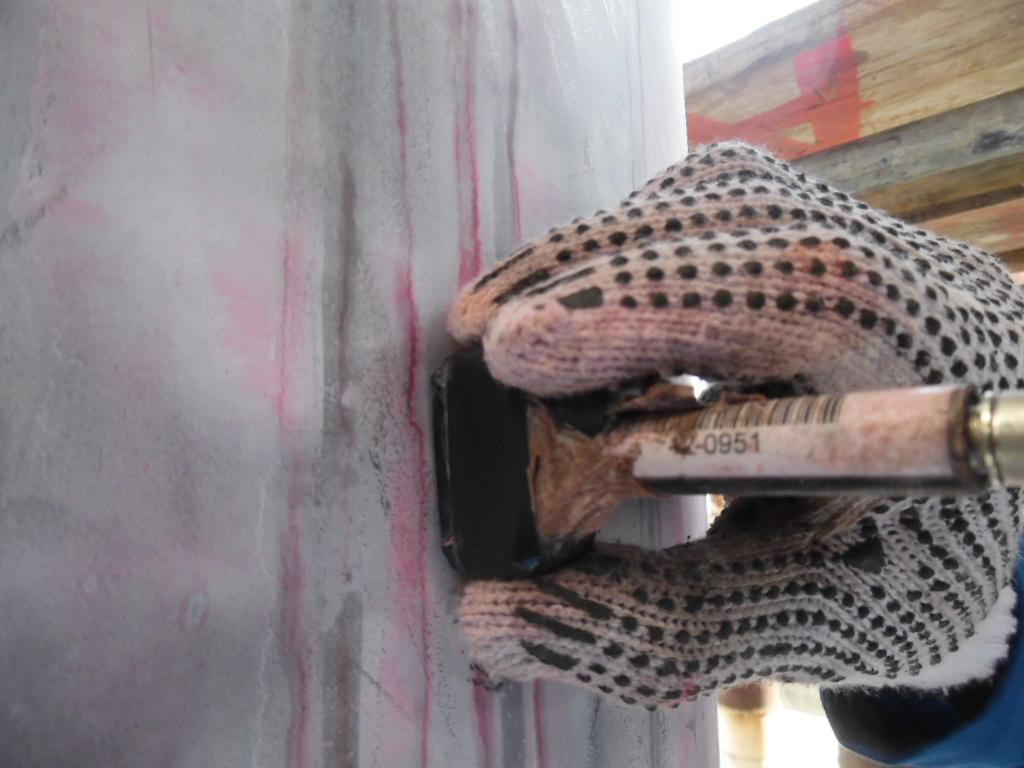
Introduction
An Ammonia production site in Trinidad contacted TesTex Inc. regarding a suspected piping leak. Based on discussions with their inspection team, they believed there were through wall defects due to suspected product outside the insulation and staining on the pipe that was revealed after the insulation was removed.An independent contractor tried using dye penetrant testing to identify cracks, but was unable to find any cracking that could be responsible for the signs of leakage. TesTex’s Hawkeye 2000 Balanced Field Electromagnetic Technique (BFET) system, was determined to be the best option for finding the suspected cracks.
Solution
The pipe is a 26” diameter 0.250” nominal wall thickness stainless steel pipe. The job of inspecting the pipe was broken up into three sections: the elbow; the straight pipe between the second and third welds; and the straight pipe from the weld to the “T.” Prior to the inspection using BFET, the pipe had been buffed as preparation for the earlier penetrant testing, so the TesTex technicians were not able to see the areas that were stained from the “leakage.” Our Hawkeye system was specifically designed to detect cracks in materials like this. Due to the Hawkeye’s sensitivity we were able to detect (20) individual flaws with two in the elbow that were found to be much more severe than the other indications.Shear wave UT was used to prove up all indications. The area with cracks presented a backwall, where the areas that were in good condition did not.
TesTex’s BFET system is able to detect surface and subsurface cracking in ferrous and non-ferrous materials. The Hawkeye requires minimal surface preparation compared to other techniques and is faster than dye penetrant testing. The system can accurately detect cracks with a scanning speed up to one foot per second. TesTex’s software can eliminate noise and liftoff signals from the flaw signal and can handle up to an eight probe array to create a wider scan path. The technology relies on two electromagnetic fields in balance with each other. The balance becomes unstable in the presence of cracking and relays a flaw signal to our software.
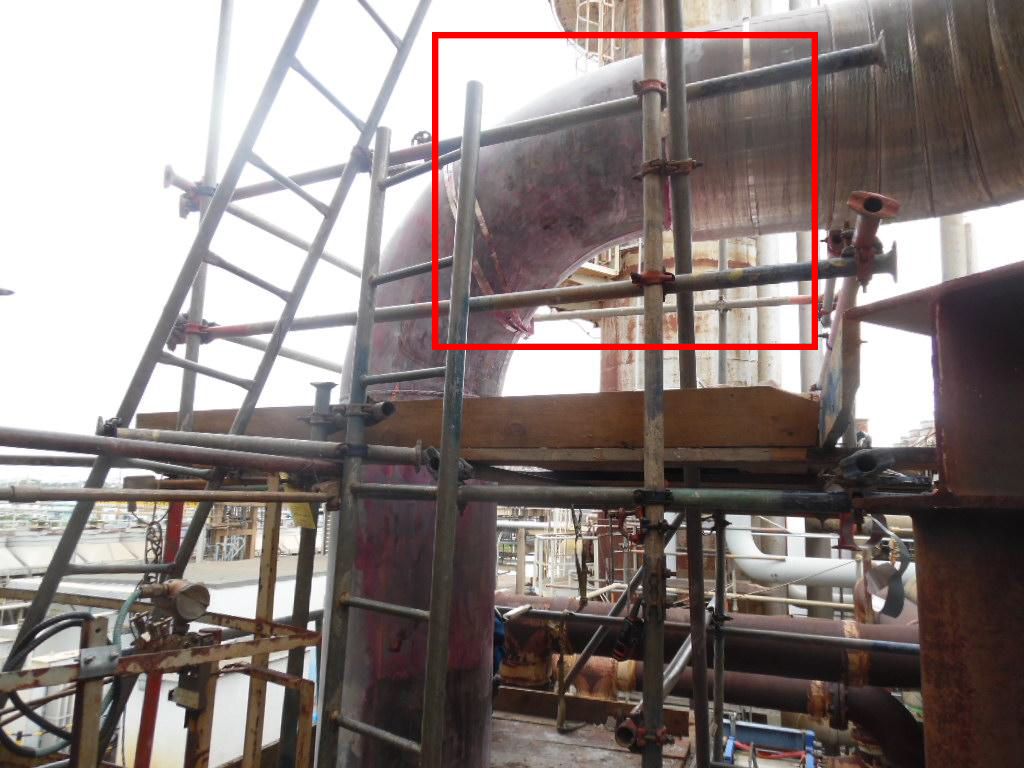
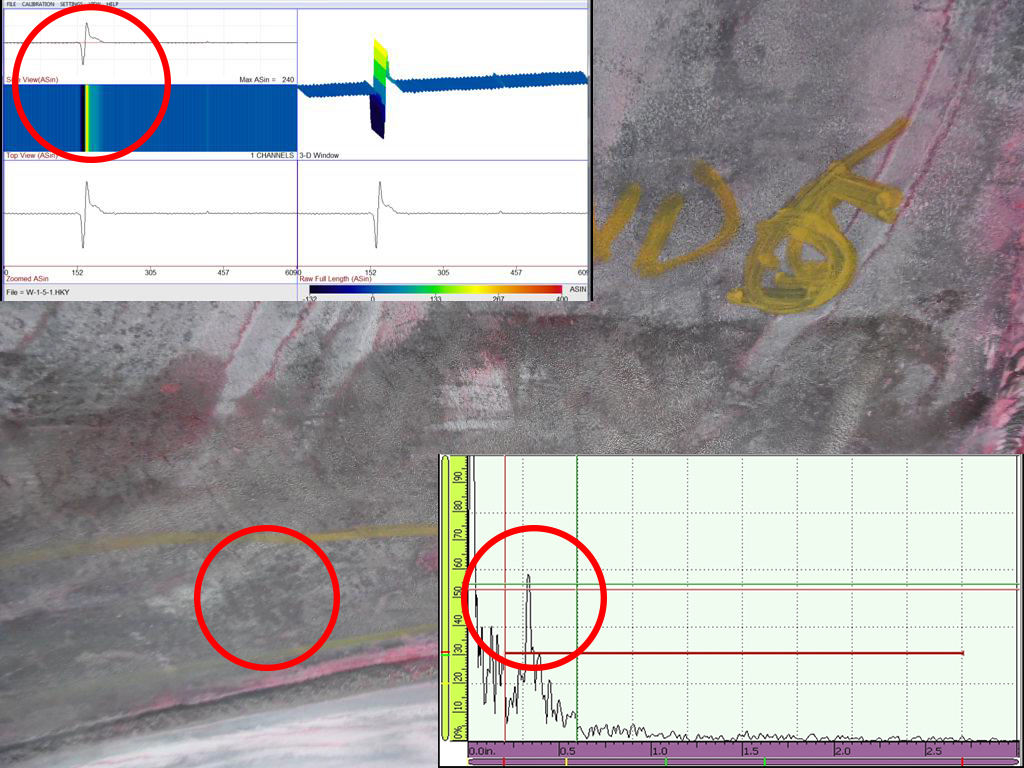
Conclusion
The production plant contracted TesTex to help find the leaks when dye penetrant failed due to our BFET technology, and our well trained staff. The Hawkeye 2000 was able to accurately identify (20) flaws, including the indication above which is believed to be the source of the leak. Once repaired, the client brought the unit online, and no further leaks were found. Our system was determined to be a fast, accurate, and cost effective tool for detecting flaws where dye penetrant could not. The outage contact indicated their appreciation for our professional conduct during the inspection and with the results.If you would like to learn more about our inspections, our systems, or how they can be used on your site, please contact us at 412.798.8990 or click here.