Superheater Pendant Crack Detection Using our Hawkeye BFET System
4/27/2016

Introduction
A local power plant in Cheswick, PA. had tube failures in their superheat pendants. Some of the hairpin tubes had ruptured causing damage to nearby pendants. After sending the failed tube off for analysis, they found that cracking was the failure mechanism and attempted to use dye penetrant to test the remaining pendants. Due to the low light and layout of the bends as well as scale buildup, visually spotting the cracks both with and without dye penetrant was not possible.TesTex acquired some of the pendant bends that had cracking, and we were able to show the plant that our Hawkeye 2000 Balanced Field Electromagnetic Technique (BFET) system could easily detect the cracking. TesTex was then contracted to inspect the superheat bends in their Unit 1 boiler.
Solution
There are (82) hairpin bends to inspect in the superheat pendants. The tubes are 304 Stainless Steel 2.50 ”O.D. x 0.180” nominal wall thickness on the straight sections and 0.165” nominal wall thickness at the bends. Due to the nature of the cracks, it was determined that scanning 10” above the start of the bends and down into the bends themselves was the best approach. The tubes were scanned longitudinally and circumferentially on both sides of the pendants.Using the Hawkeye BFET system, the TesTex technicians were able to identify one hairpin bend that had cracking. Upon closer inspection of the opposite pendant, there was evidence of steam scoring indicating the presence of the through wall crack.
The Hawkeye BFET system is designed to detect cracking in ferrous and nonferrous materials with minimal surface preparation. The technology relies on two electromagnetic fields in balance with each other. The balance becomes unstable in the presence of cracking and relays a flaw signal to our software.
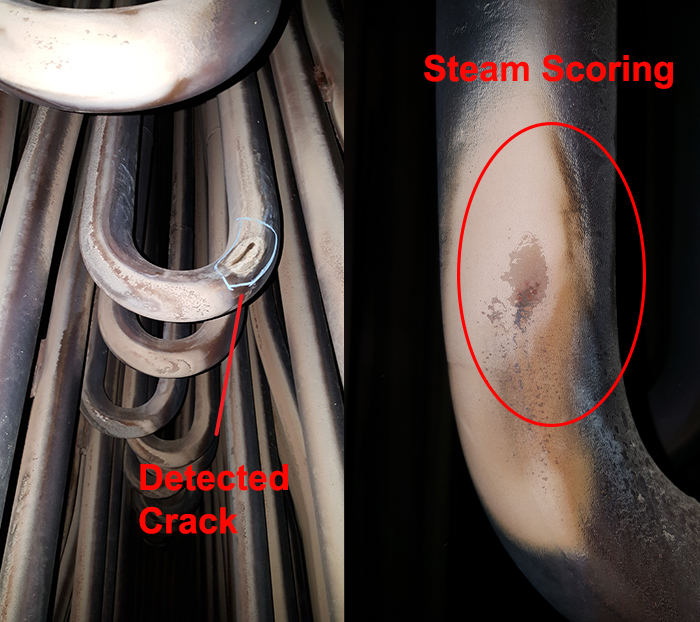
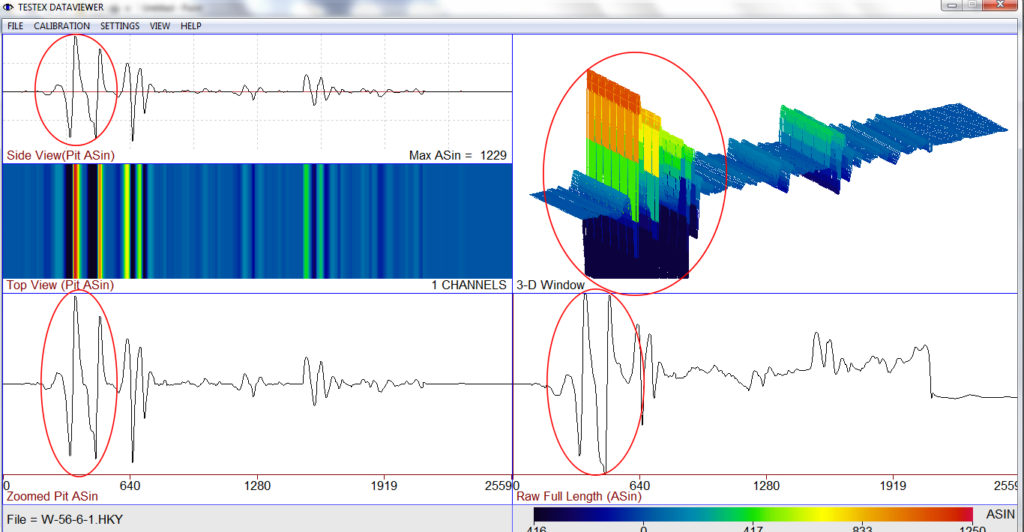
Conclusion
TesTex’s Hawkeye BFET system was able to detect a crack that was cause for a shutdown at the plant. Due to the scale buildup and the lighting conditions in the boiler, finding this one crack out of the other pendants would have been unlikely with traditional NDT methods. The TesTex Hawkeye BFET has been proven in many different settings and applications ranging from Boilers, Piping, Pressure Vessels, Columns, and even Storage Tanks. The Hawkeye BFET system is a fast, accurate, and cost effective tool for the detection of cracks.If you would like to learn more about our inspections, our systems, or how they can be used on your site, please contact us at 412.798.8990 or click here.