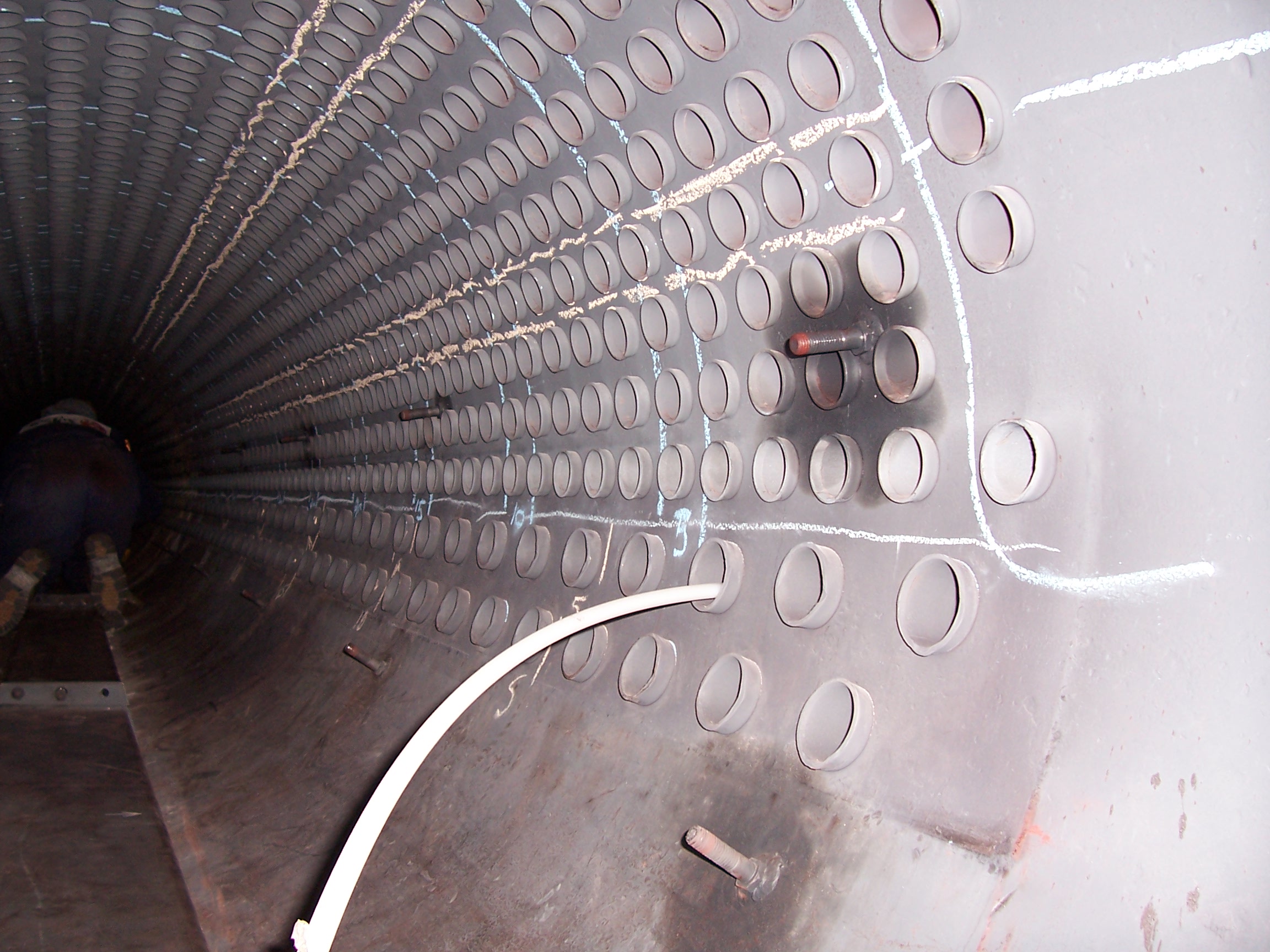
Boiler Tube Inspections
Generating Banks and Tubular Air Heaters
- TesTex, Inc. leads the way in drum-to-drum boiler inspections, employing the highly advanced Triton II RFET Inspection System. This state-of-the-art technology enables comprehensive full-length tube inspections from either the mud drum or steam drum, ensuring thorough evaluations. The Triton II RFET Inspection System features a flexible probe design, allowing for flaw detection and quantification not only in straight sections but also in the bends of generating tubes. Additionally, TesTex extends its expertise to inspect tubular air heaters when present on specific boilers. Experience the unmatched precision and reliability of TesTex’s inspection services, ensuring the optimal performance and safety of drum-to-drum boilers.
Waterwalls, Super Heaters and Reheaters
-
TesTex, Inc. leads the industry in inspecting larger industrial and utility boilers, employing the highly advanced Triton II LFET Tube Scanning System and leveraging the principles of the Low Frequency Electromagnetic Technique (LFET). This powerful combination allows for the detection of both internal diameter (ID) and outer diameter (OD) flaws on the hot side of the tube.
The Triton II LFET system facilitates a seamless and continuous 120° scan of the tube surface with a single pass of the scanner, ensuring comprehensive coverage. Any non-accessible areas, including bends, viewports, and sootblowers, that cannot be scanned are meticulously spot checked using ultrasonic testing (UT), ensuring a thorough and complete inspection.
Typically, LFET inspections in gas and oil boilers require no surface preparation, streamlining the inspection process. However, in boilers utilizing coal as a fuel source, a high-pressure water blasting may be necessary to prepare the surface for the LFET inspection.
Trust TesTex, Inc. to deliver unparalleled inspection services for larger industrial and utility boilers. Our cutting-edge technology and expertise ensure precise and reliable detection of flaws, enhancing the performance, safety, and integrity of these critical systems.
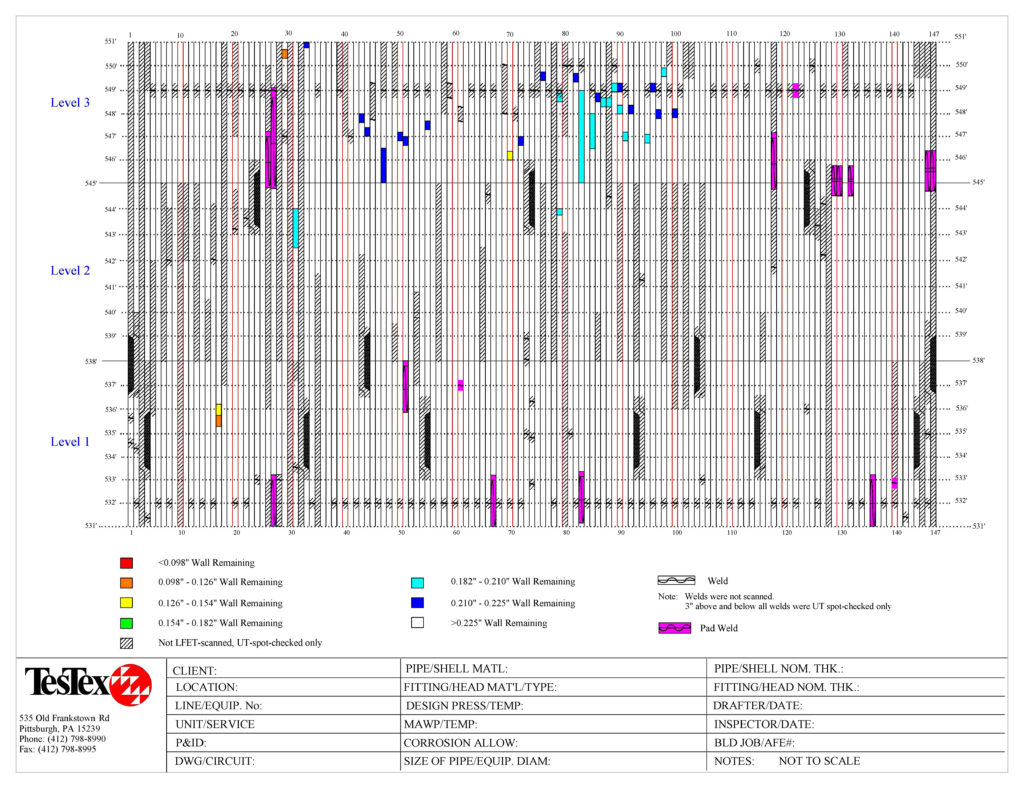
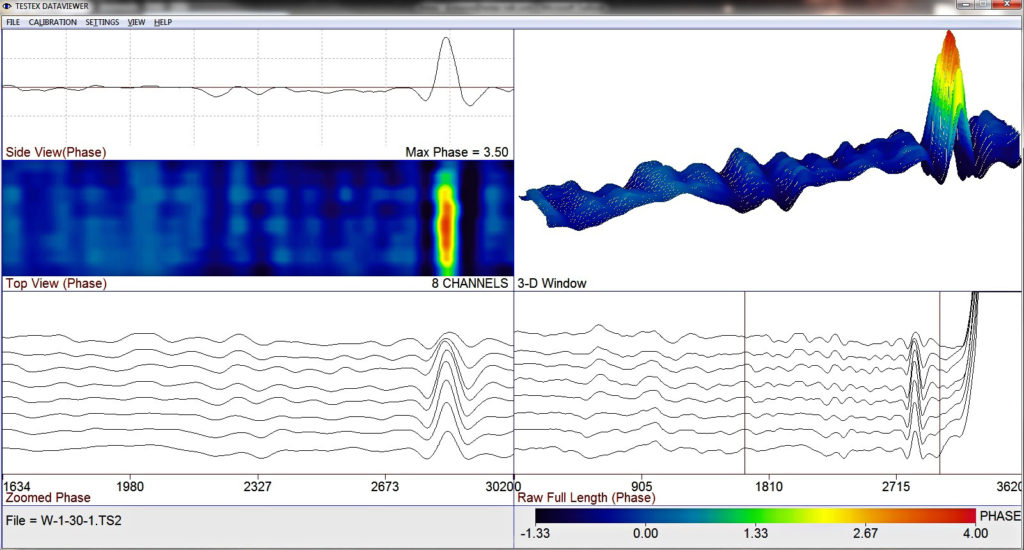
Specialty Boiler Tube Inspection Applications
TesTex, Inc. has the ability to detect the following failure mechanisms
- Graphitization
- Thermal Fatigue Cracking
- Corrosion Fatigue Cracking
- Magnetite Detection
- Near Drum Corrosion
- Please visit our Solution Providers Group page for additional information on our specialty boiler tube inspection applications.
TesTex Advantages
- RFET and LFET have the capability to inspect straight sections and bends
- 350 – 450 generating bank tubes can be inspected using RFET in a single twelve-hour shift
- 2,000 – 3,000 linear feet can be scanned using LFET in a single twelve-hour shift
- More than 40 inspection crews can be deployed at any given time
- Crews are equipped with multiple scanner/probe sizes and back-up equipment to avoid downtime
- Neither RFET nor LFET require extensive tube cleaning
- Can inspect tubing from diameters of one-half inch and greater
- Both TesTex RFET and LFET get more area coverage than the other respective techniques
- All data is collected and stored for future reference
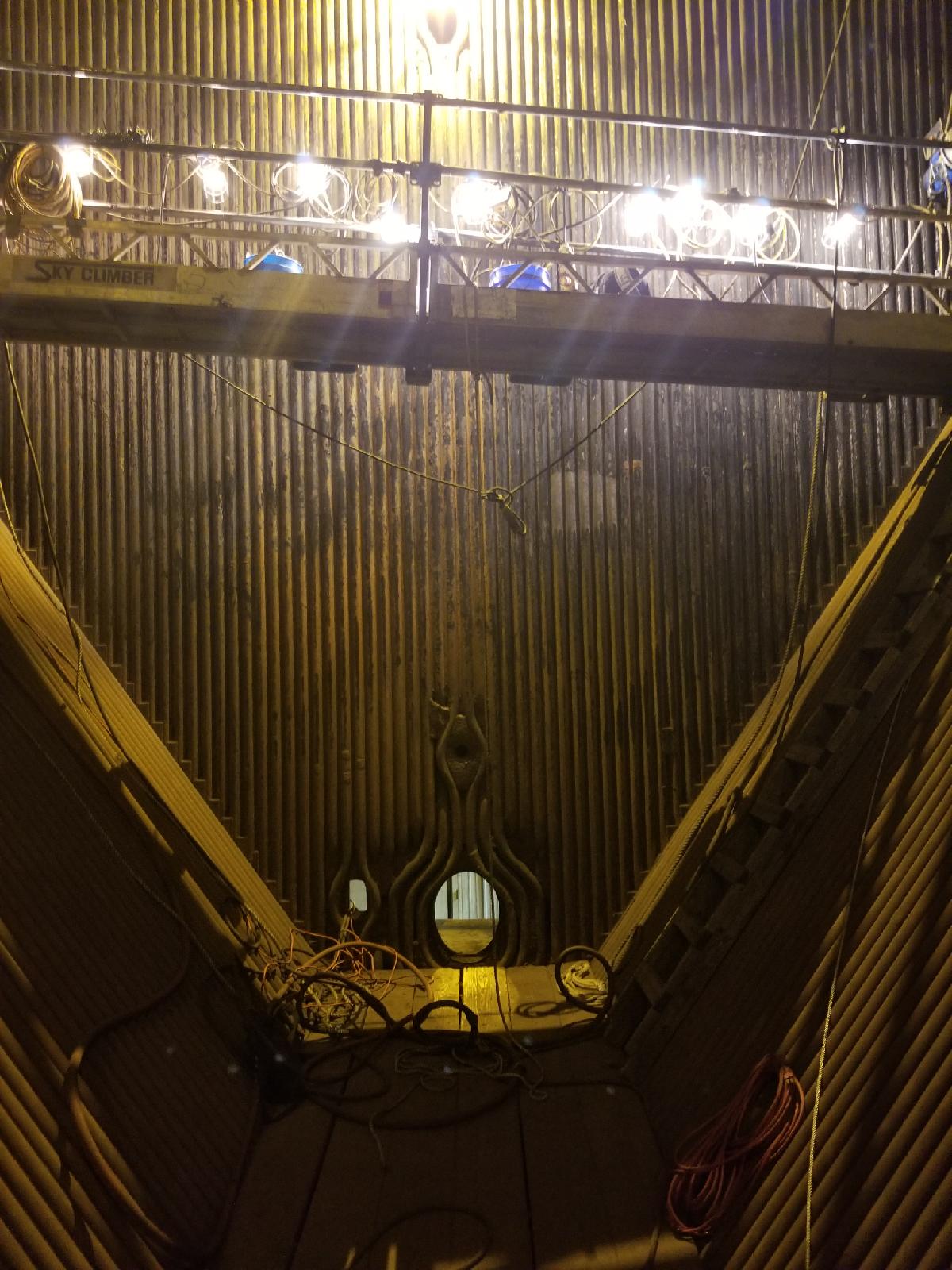
Clicking "Quote" will add the item to a temporary cart and prompt you to register/login. To view the items in this cart or send us an email requesting a quote, please complete the registration process or login.
Description | Quantity | Add to |
---|---|---|
Boiler Tube Inspection Services | ||
Triton II RFET System |